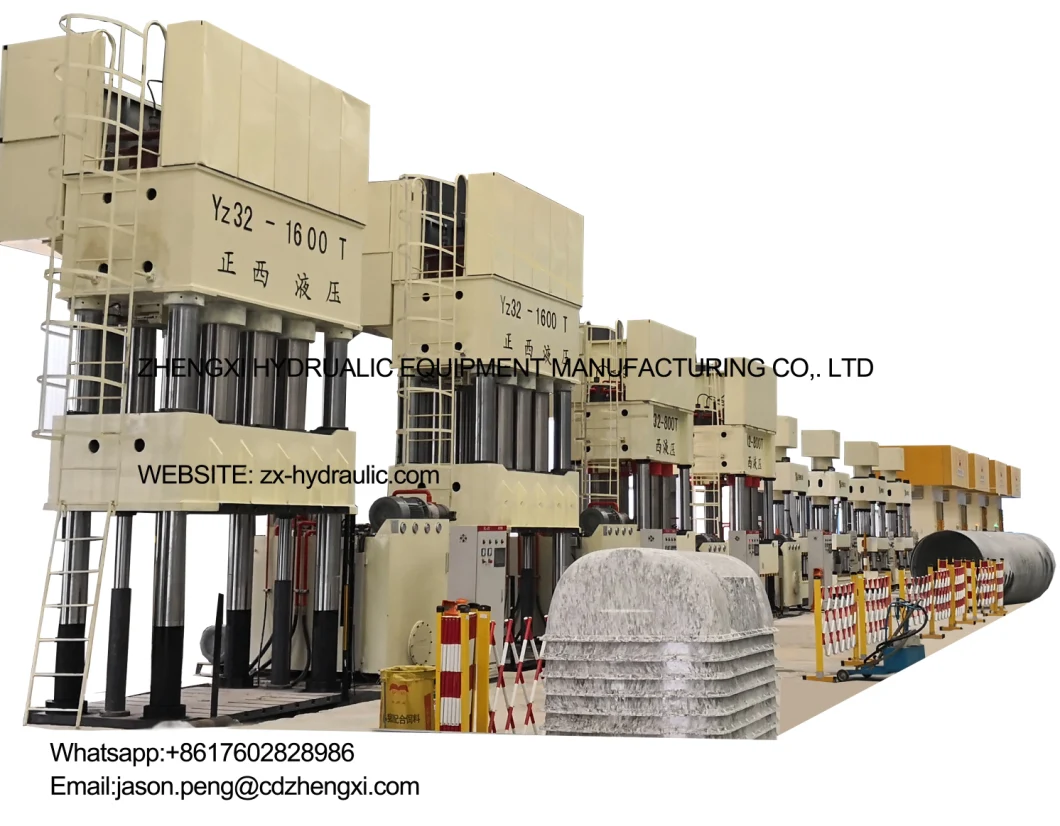
As a system supplier for forming technology, ZHENGXI integrates the specific automation solution into hydraulic, mechanical and servo press lines - from the blank to the finished part - depending on the spectrum of parts, the output capacity and the space requirements. Press interlinking can be implemented with conventional robot solutions or with the innovative Crossbar automation systems developed by ZHENGXI. Regardless of which solution is used, the transfer of the work pieces is performed without intermediate storage, with high production reliability and at high speed - directly from one die to the next.
The method of forming the composite material differs depending on the base material. Resin-based composite materials are formed by many methods such as hand lay-up, injection molding, filament winding, compression molding, pultrusion, RTM molding, autoclave molding, diaphragm molding, migration molding, reaction injection molding, and soft film expansion. Forming, stamping, etc. The metal matrix composite material forming method is divided into a solid phase forming method and a liquid phase forming method. The former is formed at a temperature lower than the melting point of the matrix by applying pressure, including diffusion welding, powder metallurgy, hot rolling, hot drawing, hot isostatic pressing and explosion welding. The latter is after the matrix is melted and filled into the reinforcement material, including conventional casting, vacuum suction casting, vacuum back pressure casting, squeeze casting and spray casting, etc., and the ceramic matrix composite material molding method mainly includes solid phase sintering and chemistry. Vapor infiltration molding, chemical vapor deposition molding and so on.
Features
1.The frame is heavy-duty as well as compact and it assures precise results.It is made of high quality mild steel and it has undergone systematicmechanical processes.
2. Electric welding of high precision
3. Usage of high-tech boring machines for extreme precision parts
4. The composite series has been designed for applications in which structural rigidity and lexibility in terms of production are the particular rerogatives required. Machines with several actions from the top or bottom or pecial solutions enable complex shapes and large dimensions to be achieved in a number of different industries.
5. It is convenient to clean and change oil.
6. Factory full set of solution
Parameters
Mold | unit | 63T | 100T | 160T | 200T | 250T | 315T | 500T | 630T | 800T | 1000T | 1250T | 1500T | 2000T | 3000T | |
Main cylinder (slider) process specs | Max.press force | KN | 630 | 1000 | 1600 | 2000 | 2500 | 3150 | 5000 | 6300 | 8000 | 10000 | 12500 | 15000 | 20000 | 30000 |
Max.return force | KN | 150 | 100 | 315 | 450 | 540 | 630 | 1000 | 1000 | 1200 | 1600 | 2100 | 2500 | 3000 | 4000 | |
Down speed | mm/s | 100 | 100 | 160 | 160 | 140 | 140 | 140 | 250 | 200 | 150 | 150 | 140 | 150 | 150 | |
Slow speed | mm/s | 20 | 15 | 15 | 15 | 12 | 15 | 15 | 15 | 15 | 15 | 12 | 15 | 12 | 12 | |
The proportion of floating pressing speed | mm/s | 20.00 | 15.00 | 15.00 | 15.00 | 15.00 | 15.00 | 15.00 | 15.00 | 15.00 | 15.00 | 15.00 | 15.00 | 15.00 | 15.00 | |
Press speed | mm/s | 10 | 10 | 10 | 10 | 7 | 8 | 8 | 8 | 8 | 8 | 6 | 8 | 6 | 6 | |
Return speed | mm/s | 120 | 120 | 120 | 110 | 95 | 100 | 100 | 150 | 150 | 120 | 120 | 120 | 120 | 120 | |
Max.stroke | mm | 400 | 500 | 500 | 500 | 500 | 500 | 600 | 600 | 600 | 600 | 600 | 600 | 600 | 600 | |
Top cylinder process specs | Max.ejection force | KN | 280 | 440 | 450 | 900 | 900 | 1250 | 1800 | 2200 | 2200 | 2750 | 2750 | 3150 | 8000 | 10000 |
Max.pull force | KN | 280 | 360 | 450 | 750 | 750 | 1250 | 1800 | 2200 | 2200 | 2750 | 2750 | 3150 | 8000 | 10000 | |
Max.stroke | mm | 150 | 150 | 150 | 150 | 150 | 150 | 150 | 150 | 150 | 150 | 150 | 150 | 150 | 150 | |
Eject speed | mm/s | 80 | 34 | 65 | 55 | 50 | 50 | 50 | 60 | 60 | 60 | 60 | 60 | 60 | 60 | |
Floating speed | mm/s | 20.00 | 15.00 | 15.00 | 15.00 | 15.00 | 15.00 | 15.00 | 15.00 | 15.00 | 15.00 | 15.00 | 15.00 | 15.00 | 15.00 | |
Return speed | mm/s | 80 | 42 | 95 | 70 | 70 | 50 | 50 | 60 | 60 | 60 | 60 | 60 | 60 | 60 | |
Upper center cylinder process specs | Max.press force | KN | 60 | 60 | 60 | 125 | 150 | 125 | 200 | 200 | 240 | 240 | 300 | 400 | 400 | 500 |
Max.return force | KN | 30 | 30 | 30 | 76 | 76 | 76 | 130 | 130 | 140 | 140 | 200 | 260 | 260 | 300 | |
Max.stroke | mm | 30 | 30 | 30 | 45 | 45 | 45 | 50 | 50 | 50 | 50 | 50 | 50 | 50 | 50 | |
Under center cylinder process specs | Max.press force | KN | 70 | 70 | 125 | 160 | 160 | 200 | 200 | 300 | 300 | 300 | 400 | 500 | 800 | 1000 |
Max.return force | KN | 40 | 40 | 75 | 100 | 100 | 100 | 100 | 200 | 200 | 200 | 260 | 315 | 500 | 600 | |
Max.stroke | mm | 150 | 150 | 150 | 150 | 150 | 150 | 150 | 150 | 150 | 150 | 150 | 150 | 150 | 150 | |
Upper floating cylinder process | Max.press force | KN | 120 | 120 | 130 | 250 | 250 | 300 | 400 | 400 | 480 | 480 | 500 | 500 | 800 | 1000 |
Max.return force | KN | 60 | 60 | 65 | 150 | 150 | 160 | 200 | 200 | 240 | 240 | 250 | 250 | 520 | 600 | |
Max.stroke | mm | 45 | 45 | 50 | 60 | 60 | 70 | 70 | 70 | 70 | 70 | 70 | 70 | 70 | 70 | |
Effective worktable size | L-R | mm | 580 | 720 | 780 | 1000 | 1000 | 1000 | 1200 | 1320 | 1400 | 1600 | 1760 | 1800 | 2000 | 2400 |
F-B | mm | 490 | 580 | 640 | 940 | 940 | 960 | 1140 | 1200 | 1200 | 1350 | 1460 | 1500 | 1600 | 1800 | |
Max.pressure of liquid | mpa | 25 | 25 | 25 | 25 | 25 | 25 | 25 | 25 | 25 | 25 | 25 | 25 | 25 | 25 | |
Max.filling height | mm | 120 | 120 | 120 | 120 | 120 | 120 | 120 | 120 | 120 | 120 | 120 | 120 | 120 | 120 | |
Main motor power | KW | 7.5 | 11.5 | 18.5 | 22 | 22 | 30 | 48 | 67 | 82 | 100 | 100 | 127 | 220 | 300 |
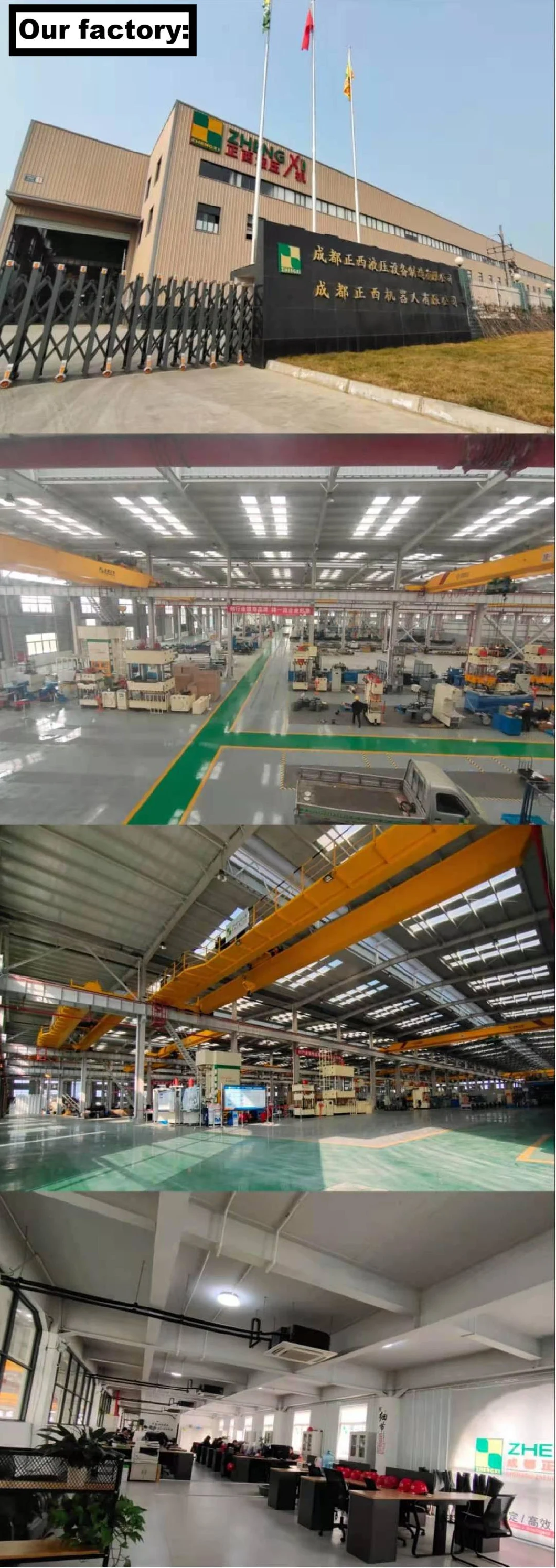
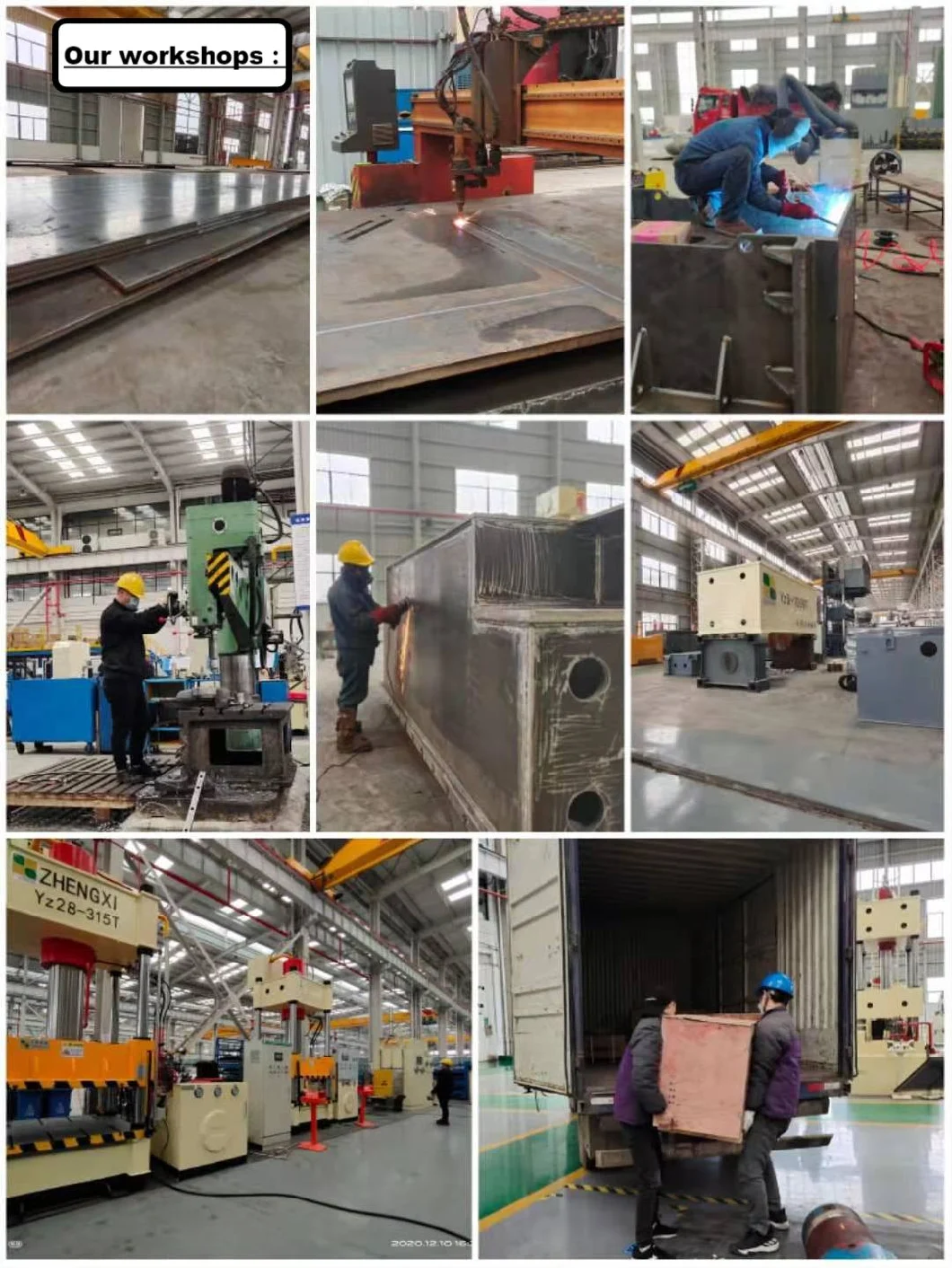
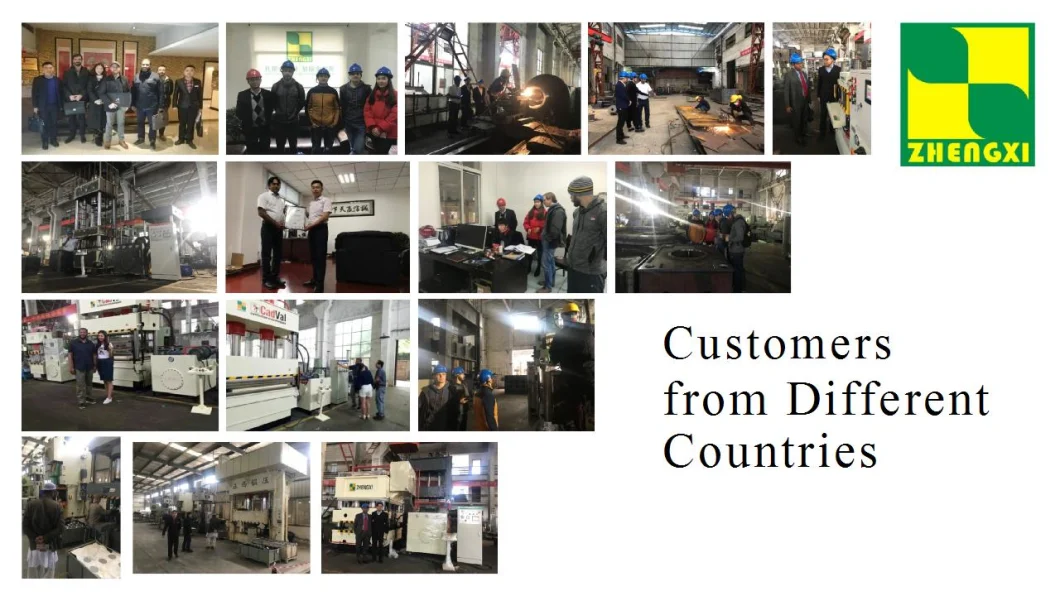
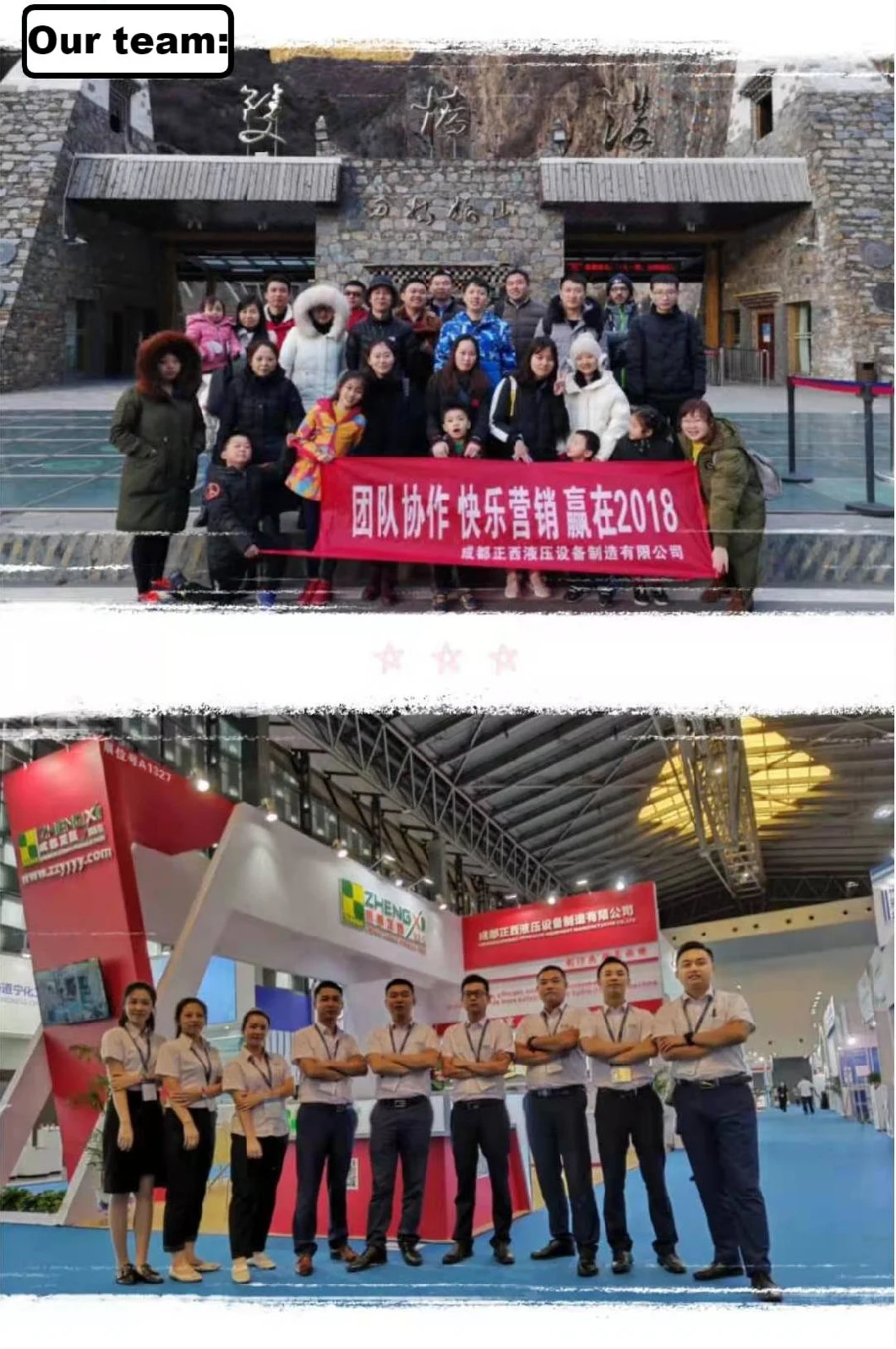
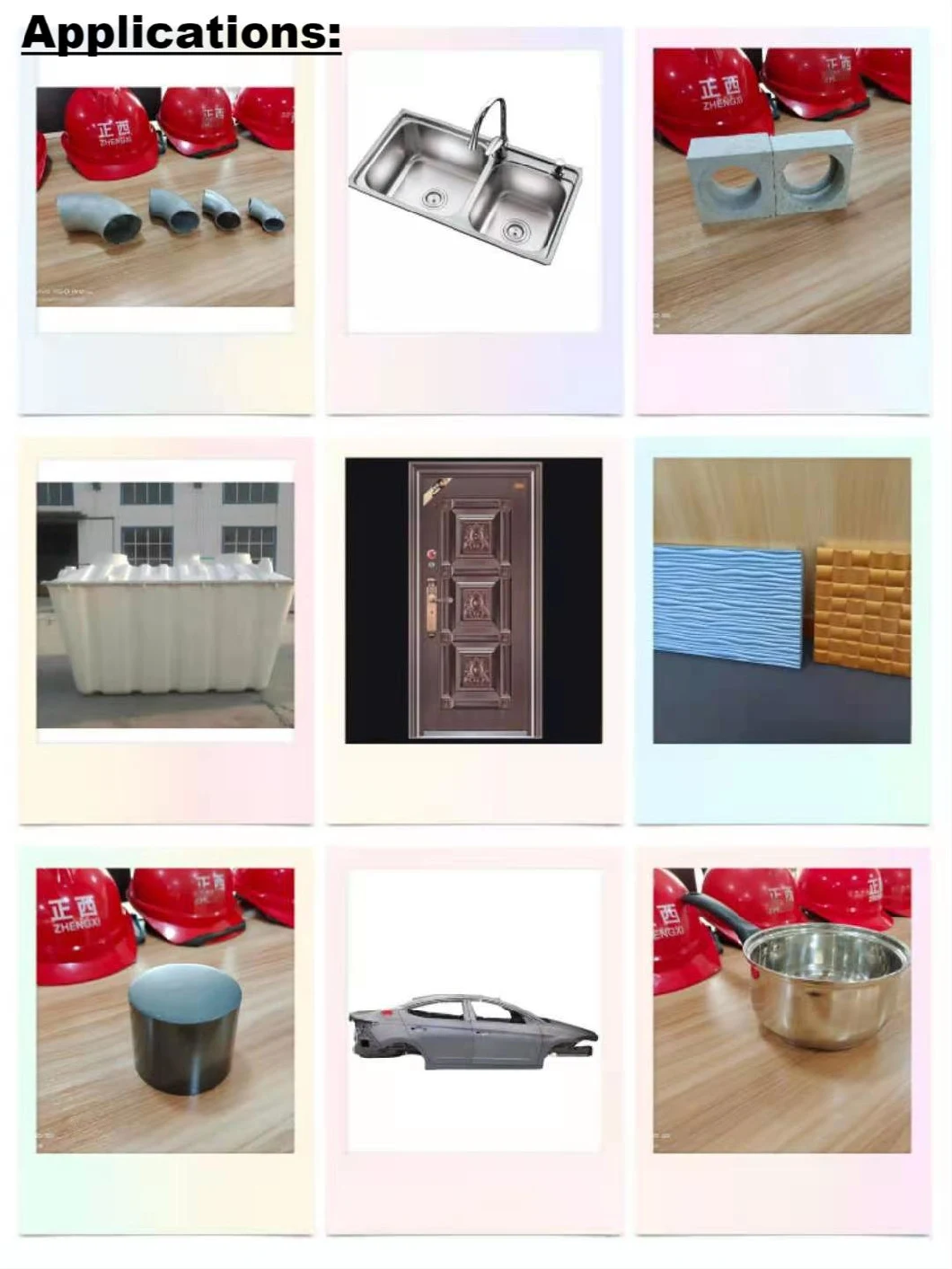
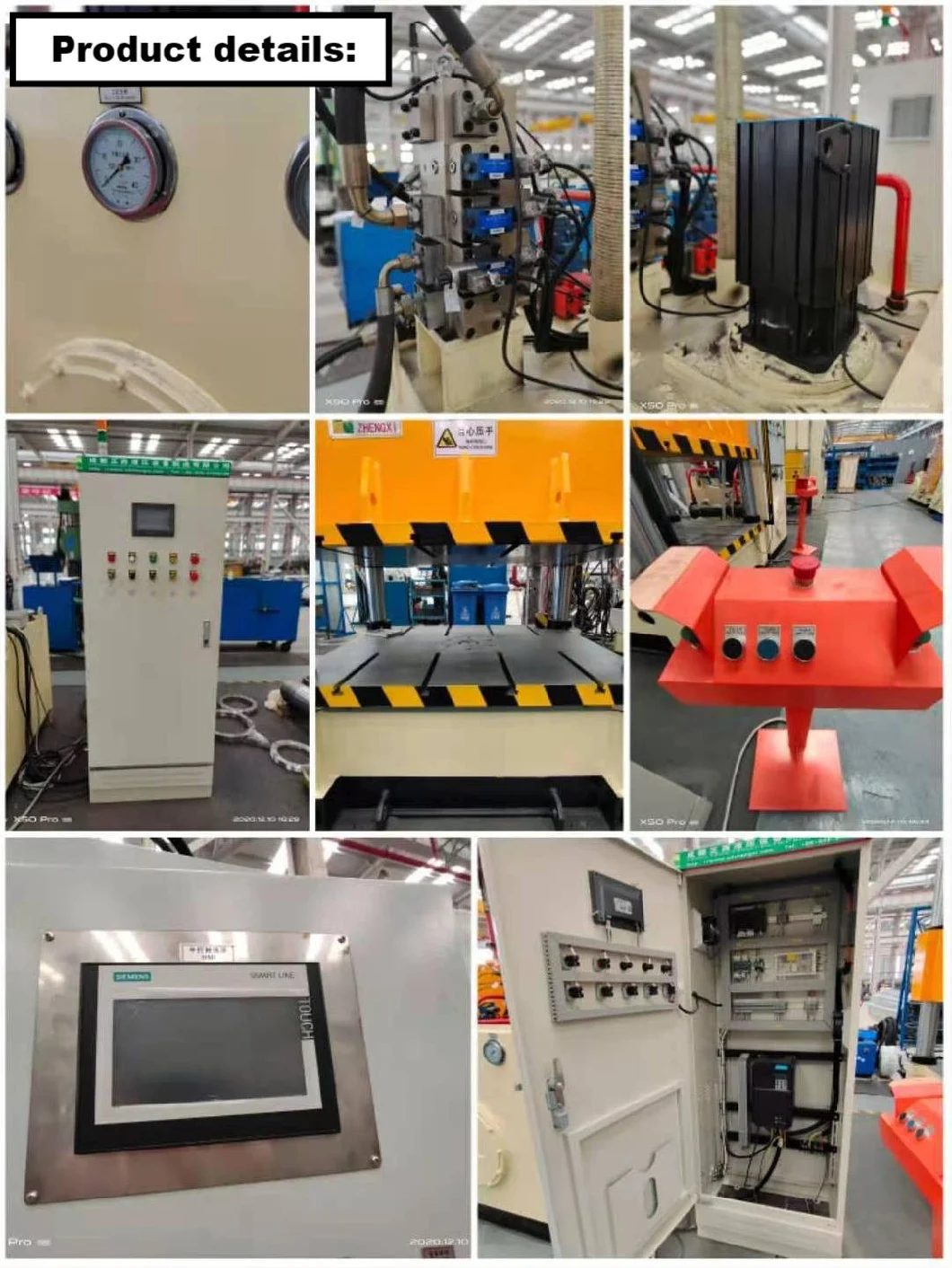
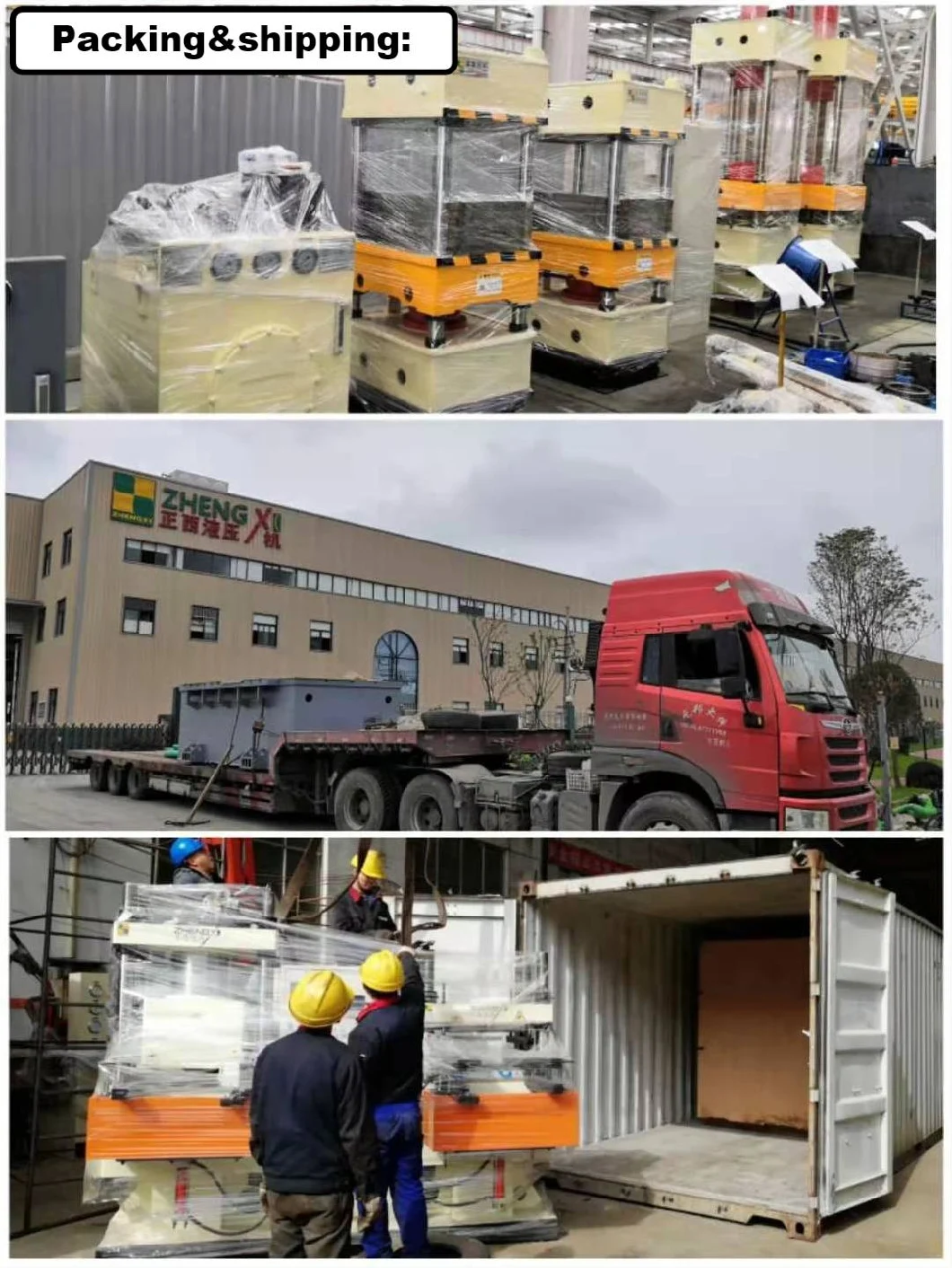
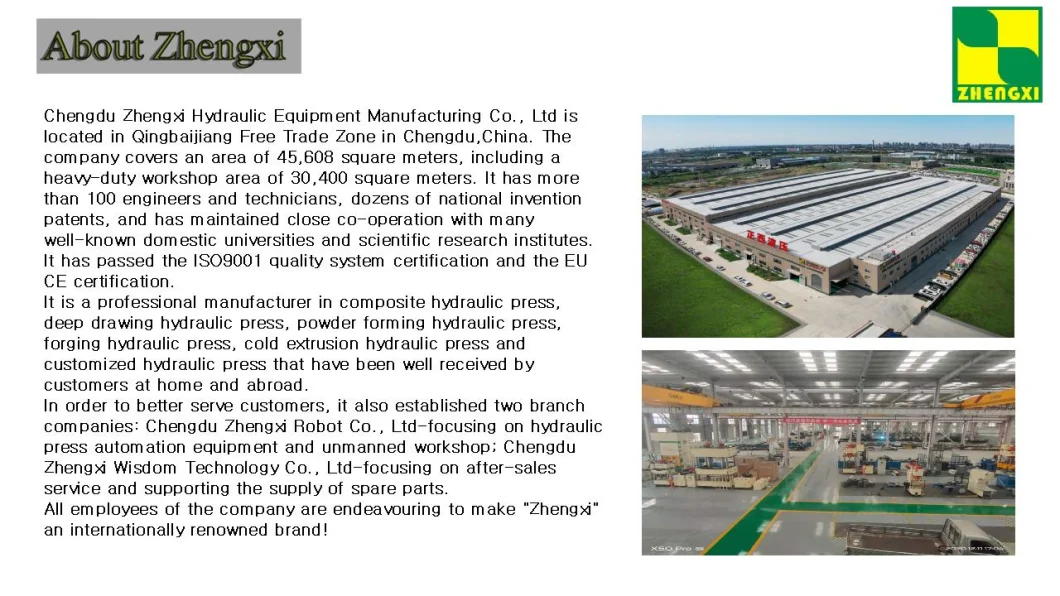
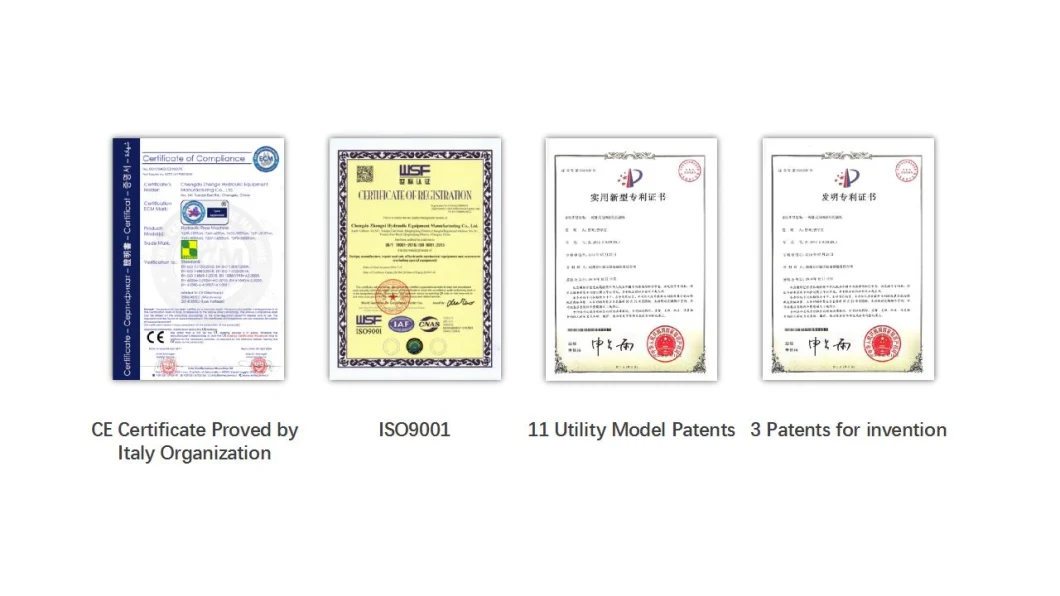
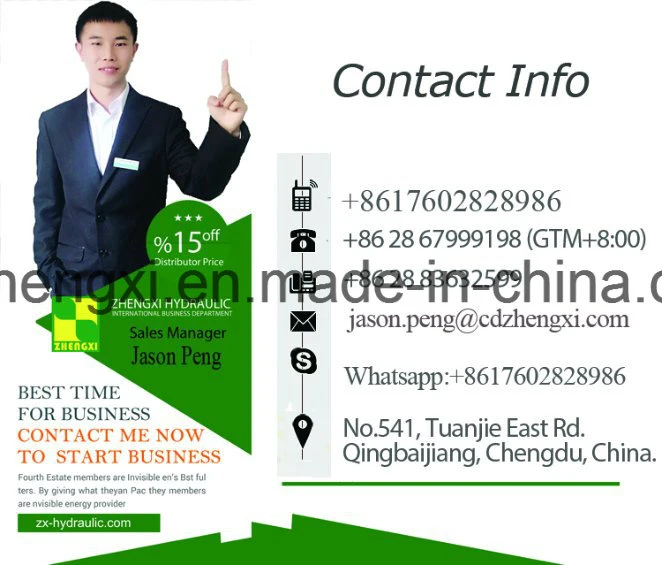
AFTER-SALE
1.Personnel training
Free training for about one week.
2. After-sale service
One year warranty.During warranty period,free maintenance service can be provided.(except man-made faults or damages arising from irresistible natural factors)
3.Installation
Customers need to pay the commission to our proffessional engineer, and travel expense is on foreign customer.(Including round ticket and accommodation cost)
Our company is an ISO 9001 certified Company, and as an approved supplier for the automotive sector, has also received the CE certificates .
A: Please tell me your specifications ,we can choose the best model for you , or you can choose the exact model .
You can also send us the products drawing ,we will choose the most suitable machines for you .
2: What's your main products of your company?
A: We specialized in all kinds of machines ,such as 1-16000Tons Hydraulic Press,SMC/BMC/GMT/DMC/LFT/GRP/FRP Press,Hydraulic Deep Drawing Press,Hydraulic Forging Press,Metalworking/Stamping Press.
3: Where is our factory located? How can I visit there?
A : Our factory is located in Jiaomei City ,Fujian Province,China. You are warmly welcomed to visit us.
4: What's the MOQ?
A: 1 set .(Only some low cost machines will be more than 1 set )
5: How about your delivery time?
A: Generally 90 days. The specific delivery time depends on the items and the quantity of your order. Sometimes we have some in stock.
6: Do you test all your goods before delivery?
A: Yes, we have 100% test before delivery.
7: How do you make our business long-term and good relationship?
A: 1.We keep good quality and competitive price to ensure our customers benefit ;
2. We respect every customer as our friend and we sincerely do business and make friends with them,
no matter where they come from.